N ear a work table at the Hybrid Atelier, UTA’s newest research makerspace, a dorukha (a two-sided shawl) sits on a dress form. Embedded with sewn lights, the shawl glows warmly in a slow pulsing pattern that reflects sensor readings from an ambient sound meter. When a wearer touches the intricate capacitive touch embroidery on the fabric, the shawl changes its rhythm, pulsing faster.
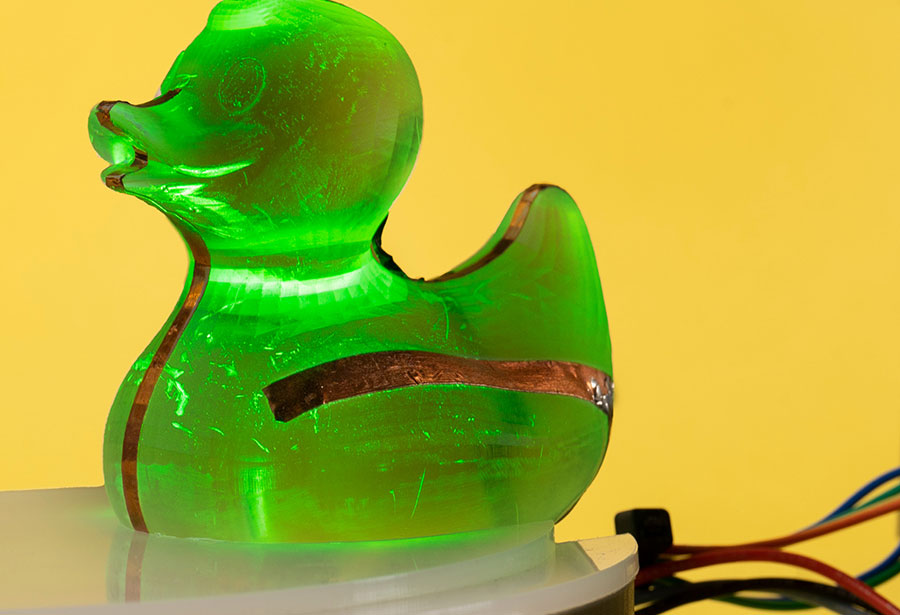
DuckCheck!
WHAT IS IT?
A resin-printed duck that helps control a coding environment
DuckCheck! is an interactive version of the “rubber duck debugging” concept of software development. The project aims to help novice programmers get into the art and science of programming by providing them with a fun and interactive avatar that can aid them in the process of coding/debugging. The duck delivers visual cues through a customizable LED and provides haptic feedback through an embedded motor. For example, the duck glows red when there is a major error in the code. These cues can help a programmer figure out errors in their debugging process and help them build better programming practices.
It’s just one of the many kinds of innovative creations you’ll find underway at the Hybrid Atelier, where students complete projects that range from electronics-infused fabrics like the dorukha to 3D-printed clay vessels and silicone bladders. The digital fabrication facility is set up for craft practices in ceramics, textiles, printmaking, and glassworking. As a research makerspace, the Hybrid Atelier contributes to a branch of computer science known as Human-Computer Interaction (HCI), which aims to understand how technology can be embedded within our everyday environments and culture.
“It’s a twist on traditional makerspaces because we’re exploring how we create new practices that other people can participate in,” says Cesar Torres, assistant professor of computer science and engineering and director of the Hybrid Atelier. “Our makerspace serves as a nexus between the arts, engineering, and the sciences.”
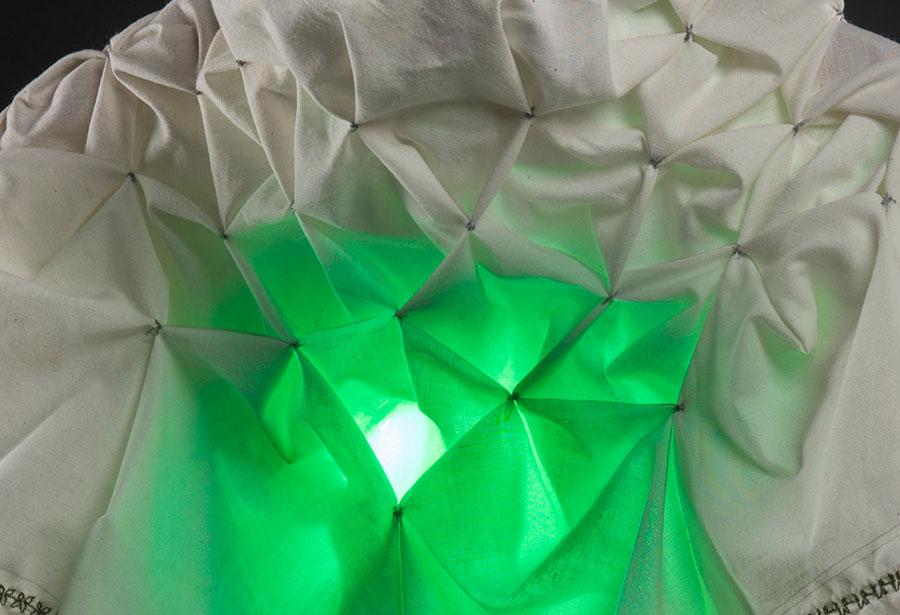
Dorukha
WHAT IS IT?
A two-sided shawl embedded with capacitive-touch embroidery and a sound meter
Dorukha, which means “two-sided” or “double-faced,” is a type of shawl that has been produced for centuries. In this modern iteration, the dorukha is made from a smock-constructed textile that has been infused with capacitive-touch embroidery and a sound meter that responds to proximity interference through an LED, which is also incorporated into the shawl.
Shreyosi Endow, who is working toward her PhD in computer engineering with a focus on HCI, became involved with the Hybrid Atelier after meeting Dr. Torres and learning about the makerspace at the Student Research Computing Festival, UTA’s annual research workshop and conference.
“The Hybrid Atelier felt like a great fit for my research interests,” she says. “I’ve been working in the lab for the past year and a half now, and it has been a great experience so far.”
Endow’s main research interests in the field of HCI include creativity support tools, digital fabrication, wearable technology, and assistive technology. While she typically focuses on developing the hardware side of project production, the interdisciplinary nature of the Hybrid Atelier has allowed her to branch out and try new things—and she has used those experiences to expand her research as well.
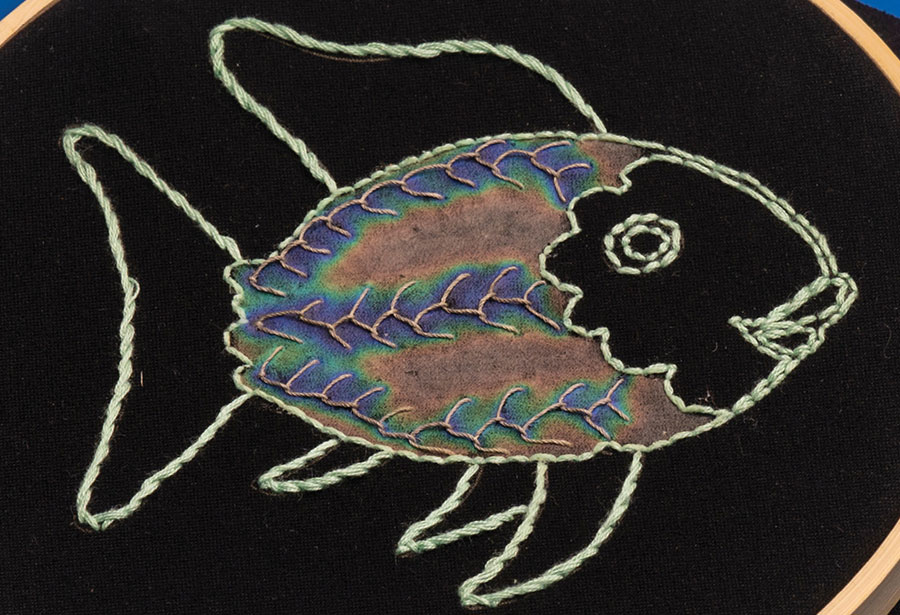
Embr
WHAT IS IT?
A hand-embroidered liquid-crystal textile display
Consisting of a resistive heating circuit made of conductive thread that activates liquid crystal ink to make dynamic color changes, these embroidered pieces demonstrate how electronics can be meaningful, customizable, and fun. The team behind the project created Embr as an engaging introduction to e-textiles and electronics.
“I was able to get my hands on a pottery wheel, and as a result, I spent an entire semester researching how to create tutorial systems for tasks, like throwing clay on the wheel,” Endow says. “Makerspaces are great for creating many opportunities to get hands-on experience and learn new skills, which is not only useful for the future, but also keeps the current learning experience inspiring and fun.”
Long Nguyen, a senior computer science major, joined the Hybrid Atelier after taking Torres’ “Intro to HCI” class. He says the class sparked his interest in interactive design and HCI, and after joining the Hybrid Atelier, that interest turned into a passion for creativity he didn’t know he had.
“A lot of people have creative interests, but they don’t know where to start or how to express them,” he says. “The Atelier is my creative home, and outside of research, I actually come back consistently to do things I never thought I would do.”
For Nguyen, that runs the gamut, including laser printing, woodworking, screen printing, weaving, and more.
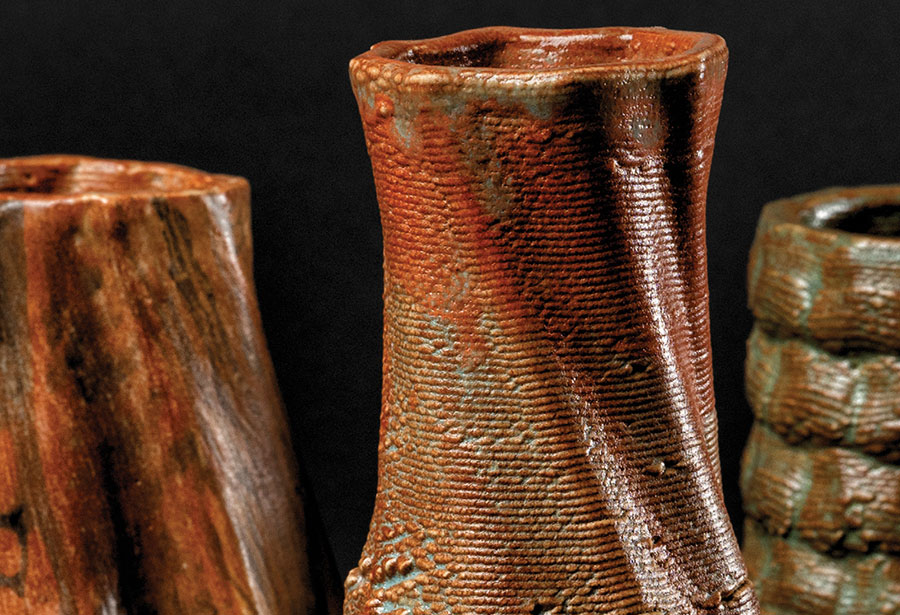
Printed Pottery
WHAT IS IT?
Individual pottery printed from a 3D clay printer
Like traditional 3D printers do with plastic, a clay 3D printer extrudes clay into shapes and textures based on .stl files. While thrown pottery can be more therapeutic, tactile, and better suited for material conversions, clay 3D-printing can achieve precision and textures much faster, making it easier for mass production and for novices to try their hand at pottery without a steep learning curve.
“Makerspaces are so important because they literally induce creativity, and then they mix creative thinking with engineering logic,” he says. “After I graduate, I’m planning on pursuing a hybrid design and engineer role, and my work at the Atelier is right in line with this. We literally merge art and code.”
As An Nguyen, an undergraduate computer science student, notes, having a place to explore more creative endeavors while developing technical skills at the same time is invaluable for any student.
“Regardless of the outcome, the making process allows you to take charge of your learning and is a very empowering experience for students,” she says. “Being part of an uplifting research community has continuously pushed me out of my comfort zone and has led to opportunities and experiences I wouldn’t have had otherwise.”
These intangible lessons are exactly the point of any makerspace, Torres says. And it’s also why they tend to thrive on university campuses.
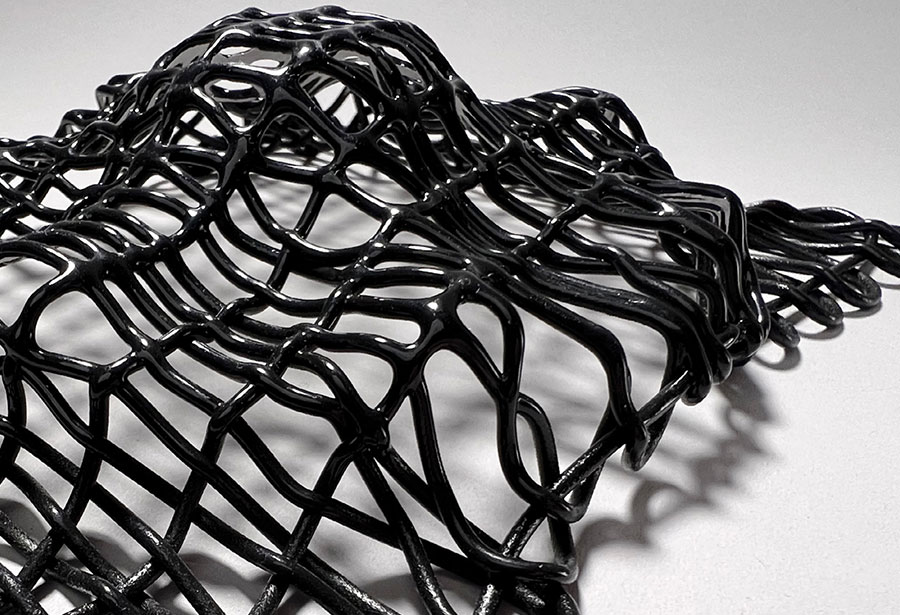
Thermofusion & Thermoslumping
WHAT IS IT?
Thermoplastics that have been manipulated, edited, and composited
Current 3D printing workflows limit a maker’s ability to alter the shape and form of a printed object and constrain the number of materials that can be used in a singular form. Leveraging techniques from traditional glass slumping and fusion, these forms demonstrate how different thermoplastics can be manipulated, edited, and composited to create expressive, functional 3D forms while still maintaining the benefits of computer-aided design.
“Makerspaces align with the pedagogy strategies that are all the rage in an experiential learning—it’s thinking through doing,” he says. “Also, the overarching aim is for students to create personally meaningful artifacts, meaning that they are working on personal projects and solving real problems within the lab community. That way, students can actually work on what they want and still learn the skills needed for their coursework.”
Endow agrees, noting that the real applications of what they learn in their classes only serve to expand the boundaries of learning.
“I think makerspaces give students a lot more autonomy and freedom in realizing their ideas than the traditional classroom,” she says. “Access to makerspaces is essential to allow students to think of new and unique applications of the concepts they learn in class and get curious about what exists outside of classes.” uta
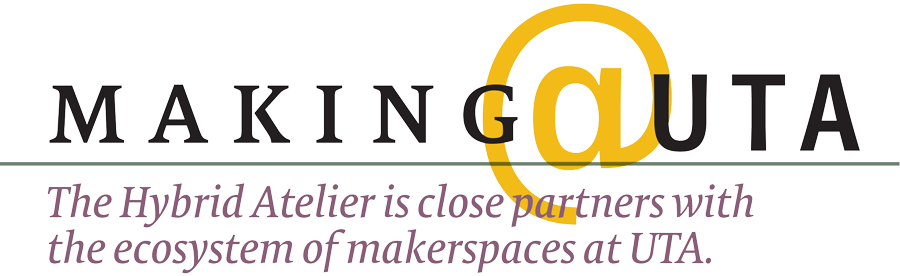
FabLab and the Studios
Located at the Central Library, the FabLab opened in 2014 and is the crown jewel of UTA’s makerspace ecosystem. Open to students, faculty, and staff, the 8,000-square-foot makerspace contains 3D printers, laser cutters, screen printers, kilns, sewing machines, and much more. Unlike other makerspaces on campus, the FabLab doesn’t necessarily prioritize academic use over recreational use.
“Our goal is to democratize the access to some of these tools so students can explore,” says Katie Musick Peery, director of the FabLab. “Our primary focus is to be a teaching space in a teaching lab so you don’t have to have any prior experience with any of the tools when you’re coming in.”
Most recently, the FabLab has grown its footprint so that the shop room contains more wood- and metal-working equipment, including traditional hand tools and CNC (computer numeric control) equipment, like a plasma cutter.
It has also grown to the Studios, which adds an additional 8,000 square feet of making and learning space. The Studios includes whisper booths for recording instrumentation and vocals; musical instruments like MIDI keyboards, guitars, and microphones; photography studios that can be utilized as green screen rooms; and a motion-capture studio that will allow students to do animation work and special effects. Other components of the space are a robotics and electronics studio with a drone cage and soldering equipment for electronic materials. In addition to the Studios, the Basement also includes a gaming-focused space, adding a social component to the area.
“People often wonder why we have these makerspaces, these creative spaces, in libraries. They think libraries, and they think of books,” says Gretchen Trkay, associate university librarian and head of experiential learning and outreach. “But libraries have always been a place for building community and getting access to resources that may not be affordable or accessible to you in your home.”
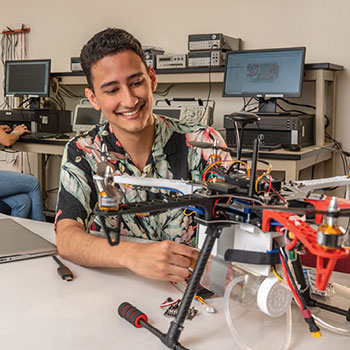
Computer Science and Engineering/Electrical Engineering Makerspace
Open to all students currently enrolled in the College of Engineering, this makerspace provides equipment for academic or personal engineering projects.
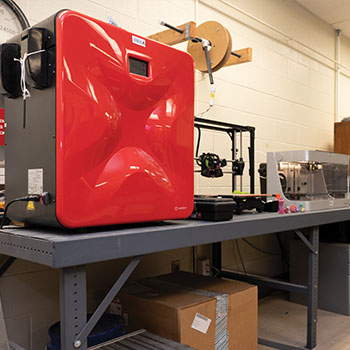
Mechanical and Aerospace Engineering Design Innovation Lab
The Design Innovation Lab in Woolf Hall is an additive and subtractive manufacturing lab that includes eight 3D printers on the additive side. On the subtractive side is a machine shop that includes a mill, lathe, drill press, metal-bending equipment, sander, bench grinder, and more.
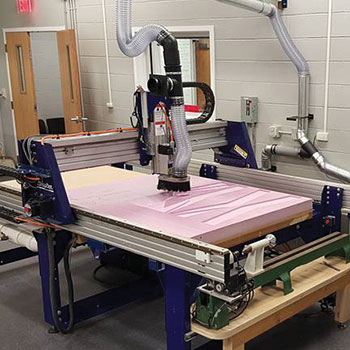
College of Architecture, Planning, and Public Affairs Digital Fabrication Lab
The Digital Fabrication Lab is a research facility focused on the testing and production of architectural components, modeling and simulation, and Computer-Aided Manufacturing (CAM) equipment. The lab is organized into two sections: One is dedicated to small prototyping production with multiple 3D printers and laser cutters; the other is designed for large-format production and holds several pieces of CNC-controlled equipment.